Commissioning, Qualification and Validation
Quality Risk Management (QRM)
At ABN Cleanroom Technology, we recognize that the successful implementation of a cleanroom facility depends on a well-structured, thoroughly planned approach. Our process covers every phase of the project, from initial process mapping to final validation and continuous monitoring, ensuring all aspects meet the highest industry standards. Quality risk management is central to our services, playing a key role in minimizing risks throughout the cleanroom lifecycle. Our commissioning, qualification & validation (CQV) team conducts detailed risk analyses and develops mitigation strategies to protect your operations. With experience across multiple sectors, we ensure compliance with ISO14644, cGMP, PIC/S, VCCN and Eudralex guidelines and regulations.
In scope for commissioning, qualification and validation:
- Cleanrooms (GMP ANNEX 1 – ISO 14644)
- Biosafety Cabinets Type I, II and III (ISO 12469)
- Operation theatres & isolation rooms
- Central Sterilization Areas
- LAF Cabinets (ISO 14644)
- Fume cupboards and fume hoods (ISO 14175-3)
- Process utilities & compressed gasses
- Isolators
- GMP Monitoring System Validation (21 CFR Part 11)
Commissioning
Following the construction phase, our commissioning process ensures a seamless transition to the qualification phase. It confirms that systems and processes are installed and operate according to design specifications and user requirements. Our proactive commissioning approach is based on science and risk, offering a fully integrated commissioning and qualification process.
A detailed Commissioning & Qualification (C&Q) Plan facilitates a timely and cost-effective qualification effort. The C&Q plan encompasses testing from FAT, testing during construction, SAT, installation testing and much of the start-up activities of a project lifecycle.
Let's talk cleanrooms
Whether you’re looking for expert advice, a quick answer, or a detailed discussion, we’re here to help. Choose the option that works best for you—call us directly, send us an email, or book a 30-minute meeting at your convenience. Let’s find the best cleanroom solution together!
E-mail us
info@abn-cleanroomtechnology.com
Call us
+32 (0)89 32 10 80
Book a meeting
Book a 30 minute meeting
Qualification
To guarantee that your cleanroom and its systems meet the specifications detailed in the URS, we conduct a rigorous qualification process after the commissioning process. Our CQV team is trained for drafting, reviewing and executing all necessary qualification documentation, including protocols, test forms and reports tailored to your project. Equipment qualification adheres to GxP guidelines like GAMP5, ISPE and ISO standards.
We tailor a testing schedule based on your specific needs, considering factors such as ISO standards, GMP guidelines, validation frequency and your URS. Our goal is to identify the most appropriate cleanroom validation tests to ensure compliance and functionality.
Guided by a clear qualification strategy defined in the validation master plan, we conduct:
Installation Qualification (IQ)
Verifies that your facility aligns with user and design requirements (as-built testing phase)
Operational Qualification (OQ)
Confirms that your systems function within defined parameters at rest (at-rest testing phase)
Performance Qualification (PQ)
Assesses your system performance under typical operational conditions (in-operation testing phase)
Validation
Validation ensures that all instruments, processes and activities consistently meet expected results. Our in-house CQV experts conduct all necessary tests according to the qualification protocols, delivering rigorous validation of your cleanroom systems. This includes verifying the sterility of processes, equipment and utilities, such as autoclave sterilization cycles.
Our comprehensive validation support ranges from document review to the development of specialized testing methods, ultimately delivering a complete package that includes protocols, sampling plans, test results, detailed reports and final conclusions. Therefore we align with regulatory guidances, including EU GMP Annex 15 Qualification and Validation, US FDA Guidance for Industry: Process Validation and ICH Q9 Quality Risk Management.
Our testing
- Recovery testing
- Particle Deposition Testing
- Temperature & humidity monitoring & uniformity mapping
- Air tightness testing (RL 10 VCCN)
- Aerosol photometer method
- Air Change Effectiveness (ACE) measurements
- Unidirectional airflow velocity measurements
- Microbial sampling
- HEPA/ULPA filter integrity testing
- Light-scattering airborne-particle counter method (LSAPC)
- Non-viable airborne particle monitoring
- Microbiological sampling
- Airflow volume measurements, air change rate calculations and airflow visualization
Monitoring
Our commitment extends beyond initial commissioning, qualification and validation. Continuous monitoring is essential to maintaining the high standards required by regulatory authorities, in line with guidelines like 21CFR Part 11 Electronic Records.
Additionally, the ICH Q7 emphasizes the significance of routinely monitoring and qualifying all utilities that can influence product quality. Meanwhile, the FDA references the ISO 14644 for determining purity limits. Both EMA and FDA also underscore the necessity of maintaining air purity, especially in the “at rest” state of cleanrooms. Another important standard, ISO 8573, which deals with compressed air, should be harmonized with the ISO14644 class limits for consistent application. Our team offers ongoing support to keep your cleanroom compliant and functioning effectively, ensuring that your operations remain in full regulatory compliance.
Our industries
At ABN Cleanroom Technology, we know that every industry demands a unique approach to contamination control and environmental precision. Our productised cleanroom solutions are engineered to meet all the required standards. Explore our tailored cleanroom environments, each designed with specific features to ensure optimal performance, quality, and compliance in your industry.
High-Tech
High-Tech
Particle-free
Temperature Control
Humidity Control
ESD Protection
Laminar Flow
Life Sciences
Life Sciences
Aseptic
Controlled Environment
Laminar Flow
Temperature Precision
Contamination Control
Pharma
Pharma
Sterile
HEPA Filtration
Pressure Differentials
Validation
Regulatory
Manufacturing
Manufacturing
Customizable
Robust
ISO Compliance
Controlled Environment
Quality Control
Food processing
Food processing
Sanitary
Easy-Clean
Food-grade
Contamination Control
Regulatory Compliant
Battery
Battery
Temperature Control
Humidity Control
Explosion-proof
Process-specific
Safe Design
What our clients say

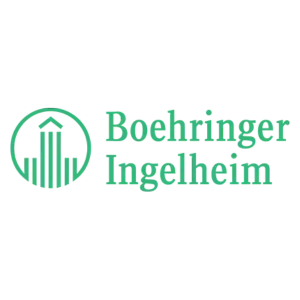
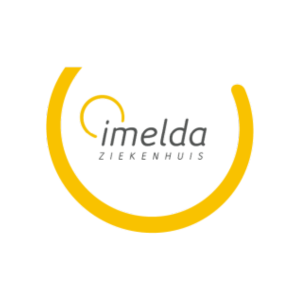
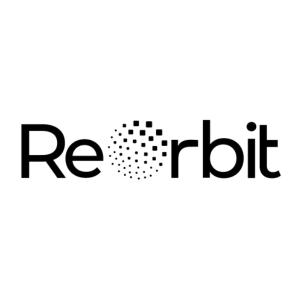
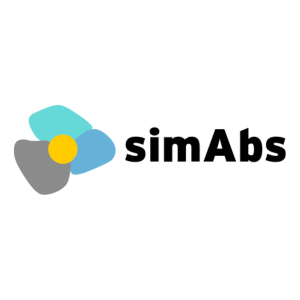
Where you can find our productised cleanroom solutions

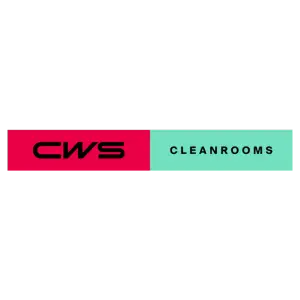
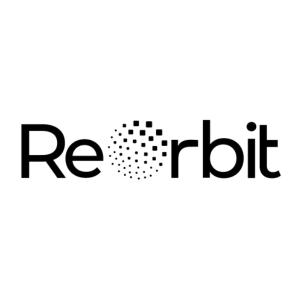
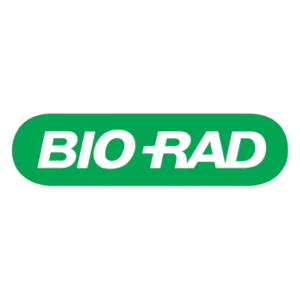
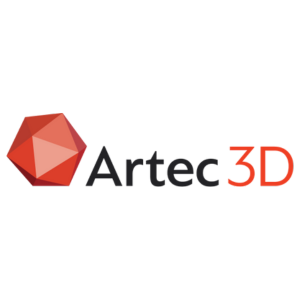
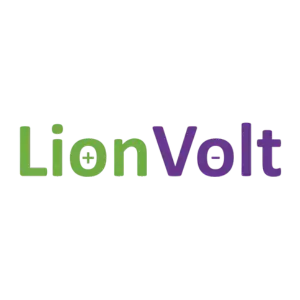
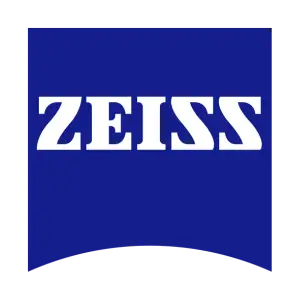
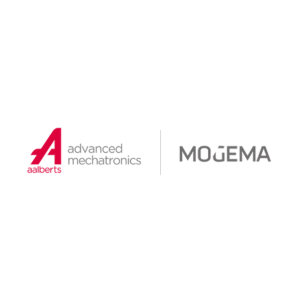
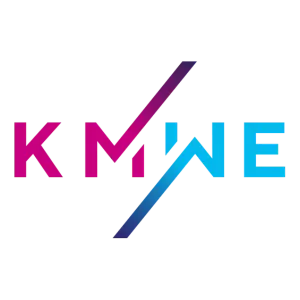
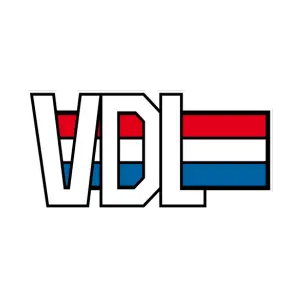
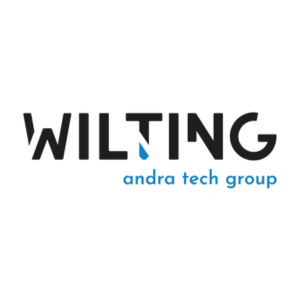
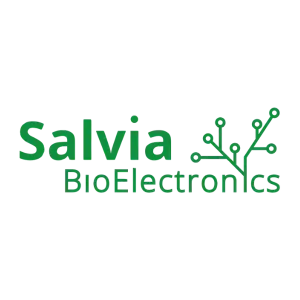
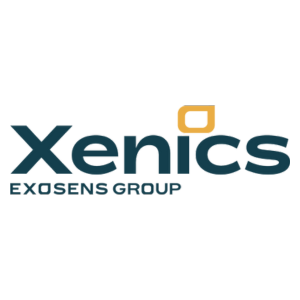
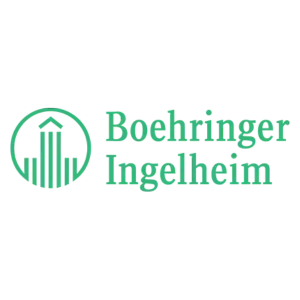
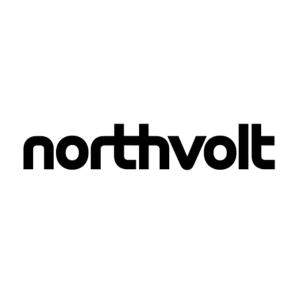
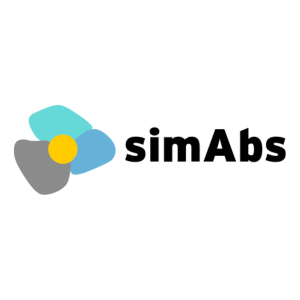
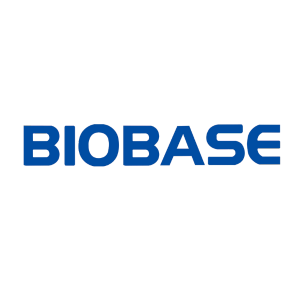
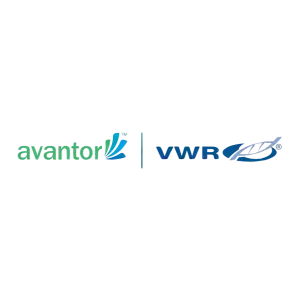
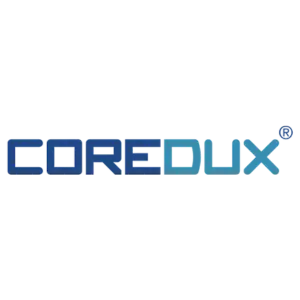
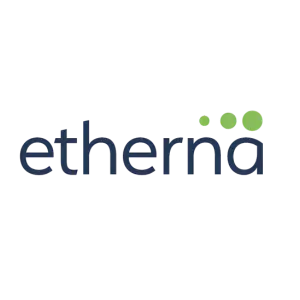
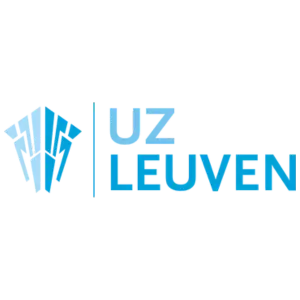
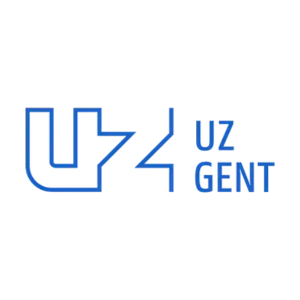
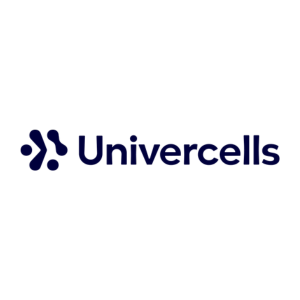
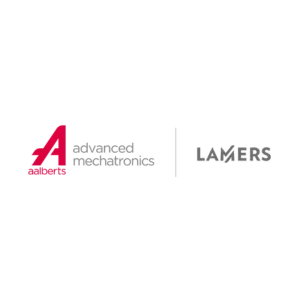
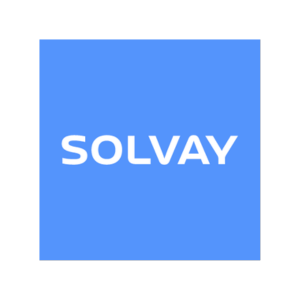
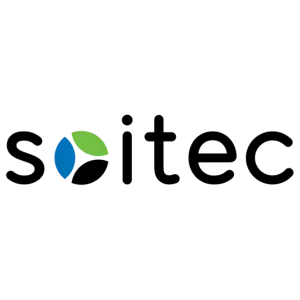
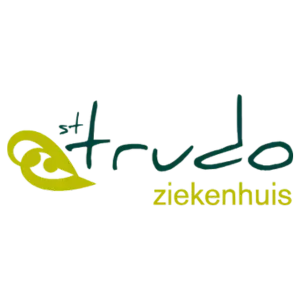
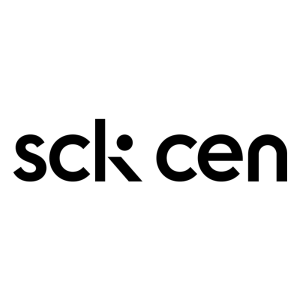
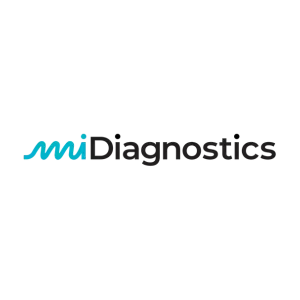
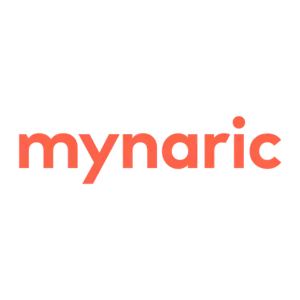
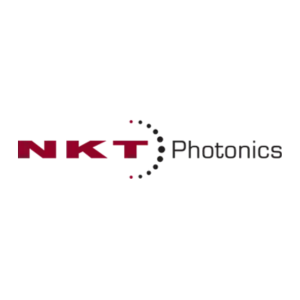
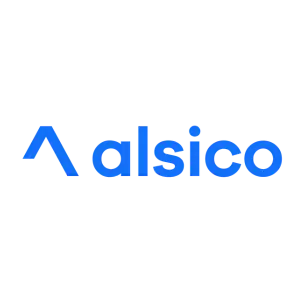
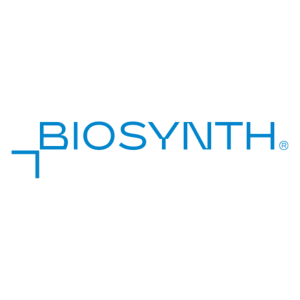
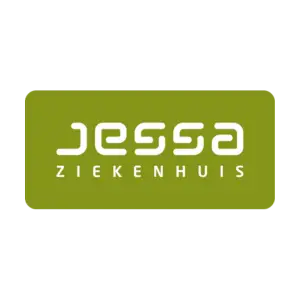
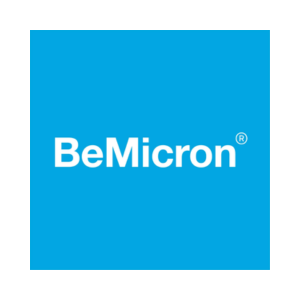
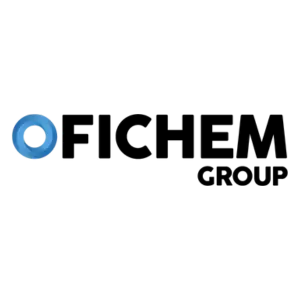
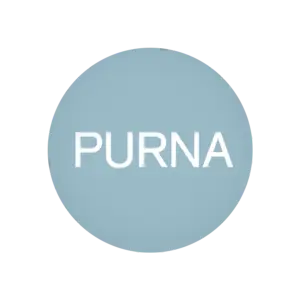
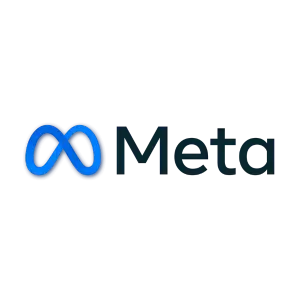
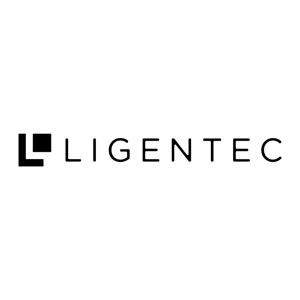
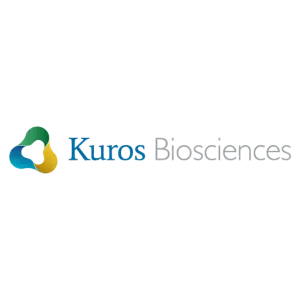
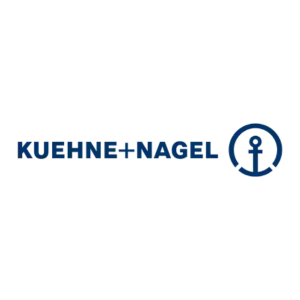

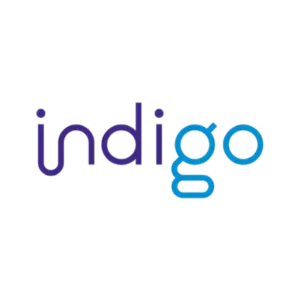
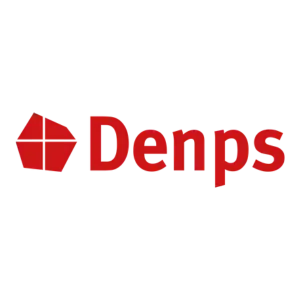
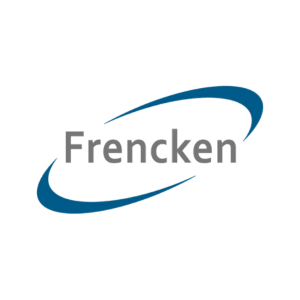
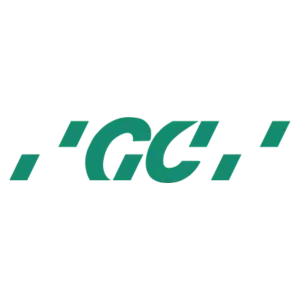
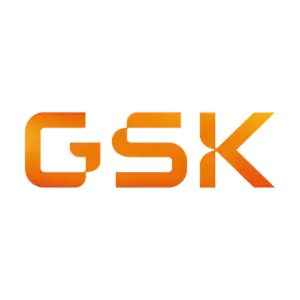
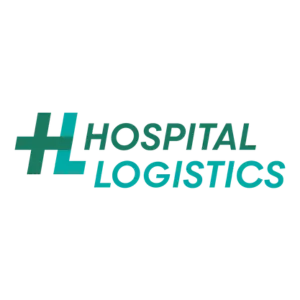
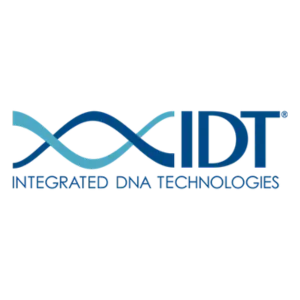
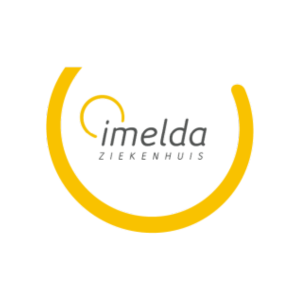
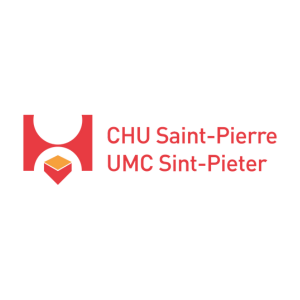